Environment
Recycling Resources
Reducing Waste and Recycling Resources
To make effective use of limited resources, Kaneka seeks to reduce and recycle industrial waste from our operations through the 3Rs (*1). We have been able to achieve zero emissions (*2) for 16 consecutive years. We are also working toward all Group companies in Japan being able to achieve zero emissions. In addition, we are working to use our resources effectively based on our new target of improving the resource recycling rate (*3) for the Kaneka Group by 1% each year.
*1 3Rs refers to reduce, reuse and recycle.
*2 Zero emission definition by Kaneka: The final landfill waste must be less than 0.5% of the generated waste.
*3 Recycling rate: Volume of generated industrial waste that is recycled (total figure for industrial waste that is subject to reuse, recycling or heat recovery).
Reducing Industrial Waste Sent to Final Landfill and Increasing Recycling Rate
In fiscal 2022, Kaneka Group generated 93,092 tons of waste, a decrease of 5,403 from the previous fiscal year. The main reasons for this were lower waste generation due to reduced production volume and the product mix, and a lower volume of soot and dust generated achieved by curbing the amount of coal used at night and reducing the amount of coal ash.
We effectively achieved zero emissions, with a final landfill volume for Kaneka of 23.7 tons, equivalent to a final landfill rate of 0.038%. For 47 Group companies in Japan, final landfill volume was down by 60 tons year on year, resulting in a final landfill rate of 1.8%. As a result, the final landfill rate for Kaneka and Group companies in Japan was 0.37%, effectively achieving zero emissions.
The final landfill volume of 16 overseas Group companies was 4,234 tons, a decrease of 876 tons from the previous fiscal year.
In fiscal 2022, Kaneka Group recycled 52,888 tons of waste. The recycling rate of waste for the Kaneka Group improved 0.5% from 56.3% in fiscal 2021 to 56.8%.
Waste Generated
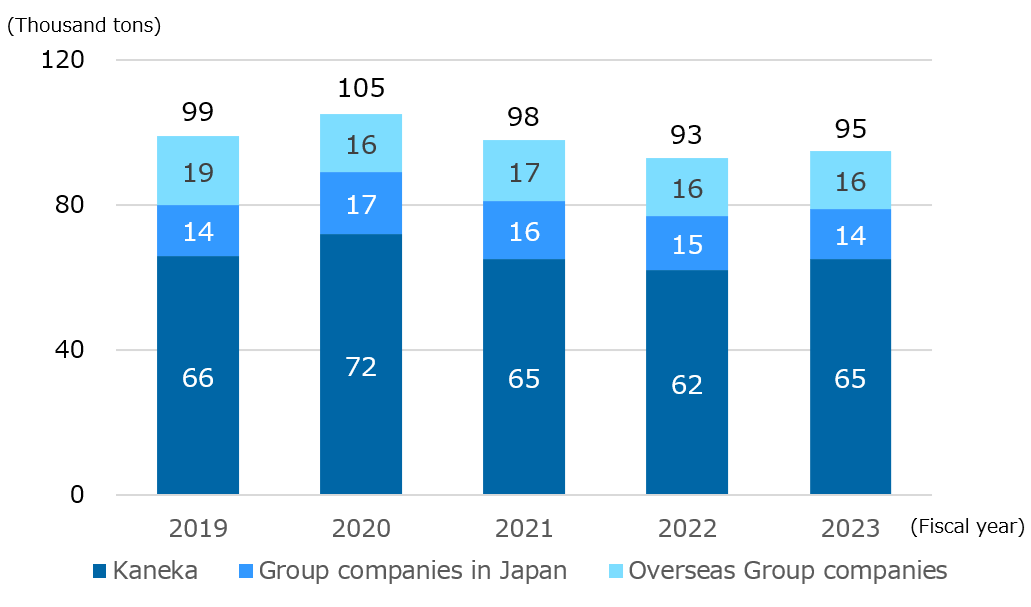
Volume and Rate of Waste Sent to Final Landfill
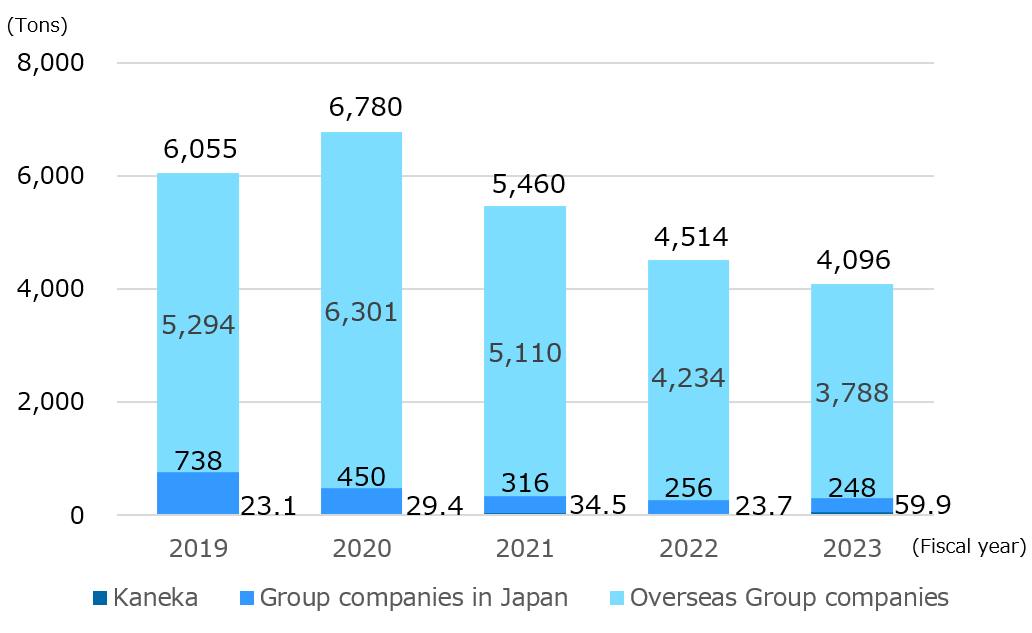
*4 The rate of waste sent to final landfill for fiscal 1996 was incorrect due to a rounding error. The second digit after the decimal point was incorrect and has therefore been revised.
Waste Recycled
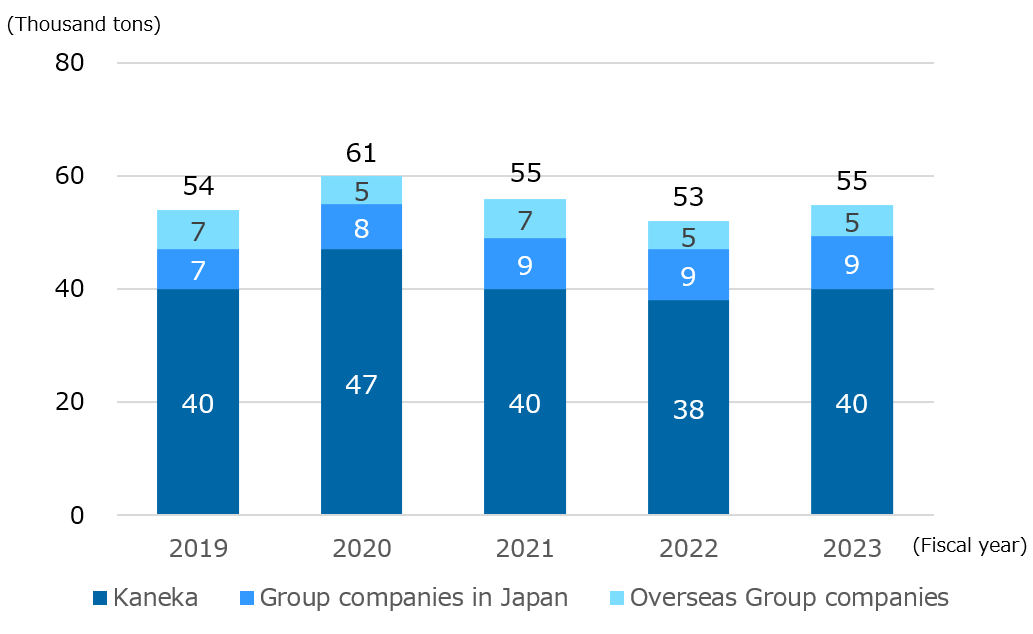
Waste Flow: From Generation to Landfill (Fiscal 2022 results at Kaneka)
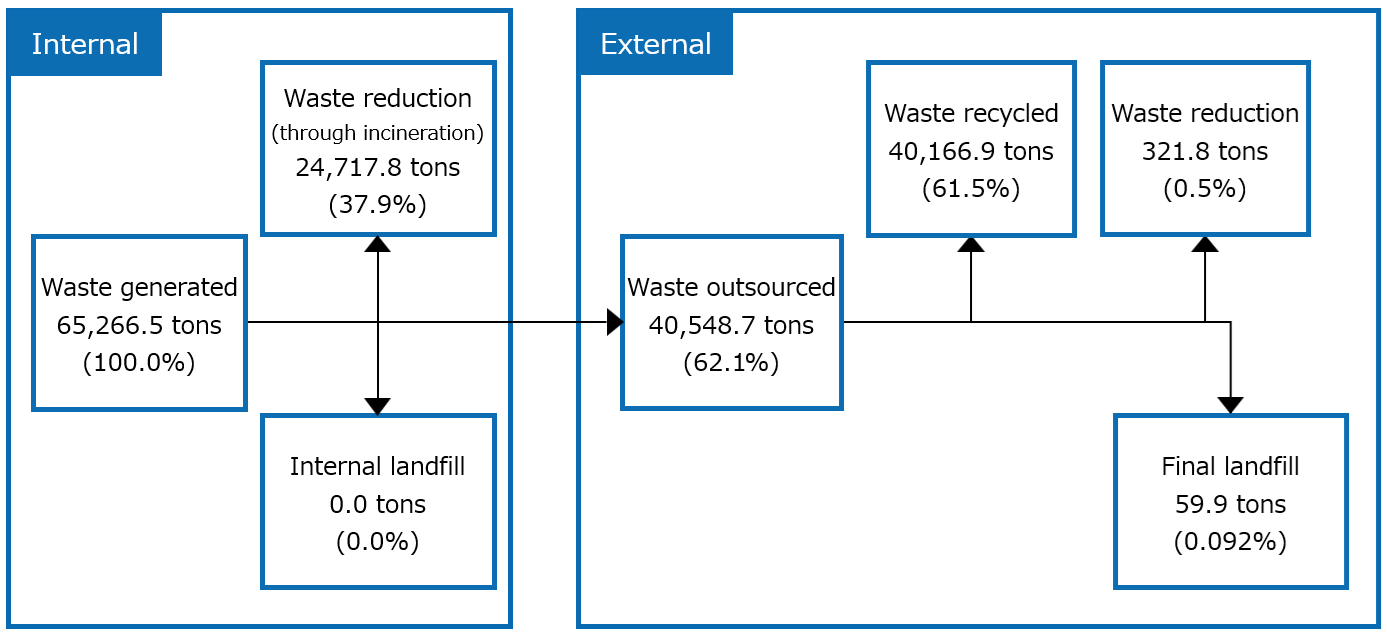
Waste at Kaneka
(Fiscal Year) | 2018 | 2019 | 2020 | 2021 | 2022 |
---|---|---|---|---|---|
Final landfilled (Tons) | 2.2 | 23.1 | 29.4 | 34.5 | 23.7 |
Final landfilled (%) | 0.003 | 0.035 | 0.041 | 0.053 | 0.038 |
Waste generated (Tons) | 67,902 | 65,917 | 72,402 | 64,864 | 62,031 |
Waste Recycled (Tons) | 42,711 | 40,060 | 47,421 | 39,719 | 38,016 |
Proper Disposal of Industrial Waste
In fiscal 2022 as well, while considering the effect of COVID-19, we visited waste disposal subcontractors that allowed on-site visits and conducted surveys based on a checklist.
Response to the Plastic Resource Circulation Act
Status of Plastic Waste Generation and Reduction Targets
The amount of plastic waste generated, which was disposed of by outsourcing it as industrial waste was 1,742.8 tons at Kaneka and 2,786.4 tons at Group companies in Japan. Kaneka is working to reduce emissions and improve recycling rates with an initial goal of reducing the amount of plastic waste generated by 1% per year.
Status of Plastic Waste Generation (Fiscal 2022)
(Tons)
Waste generated | Waste recycled | Waste incinerated | Landfill | Recycling rate (%) | |
---|---|---|---|---|---|
Kaneka | 1,742.8 | 1,599.2 | 142.4 | 1.2 | 91.8 |
Group companies in Japan | 2,786.4 | 2,354.6 | 350.0 | 81.9 | 84.5 |
Total | 4,529.3 | 3,953.8 | 492.4 | 83.1 | 87.3 |
Providing Environmental Education on Resource Recycling
We provided e-learning-based environmental education for employees of Kaneka and Group companies in Japan. The modules covered the basic concept of a circular economy, Kaneka’s policies and initiatives on resource recycling, and compliance with laws related to plastic resource recycling. Of the 5,486 employees eligible to take the e-learning course, 4,266 did so, an attendance rate of 77.8%.
In the feedback from employees who completed the e-learning course, 97% said they had developed a good overall understanding of the subject. There were many comments expressing an interest in learning more about examples of resource recycling efforts around the world and at other companies and specific examples of product design and voluntary recovery and recycling.
Environmental Education Participants and Attendance Rate
Number of employees eligible to attend | 100% participants | Attendance rate | |
---|---|---|---|
Kaneka | 4,459 | 3,344 | 75.0% |
Group companies in Japan | 1,027 | 922 | 89.8% |
Total | 5,486 | 4,266 | 77.8% |
Promotion of the 3Rs
We are taking actions across the company to reduce waste, recognizing that this ties into the maintaining and improving the natural environment in terms of saving resources, cutting costs, and reducing CO2 emissions, among other benefits.
Kaneka and Group companies in Japan are pursuing activities to reduce waste and recycle materials, mainly through a 3R approach at our various production facilities. We also facilitate continuous improvement activities through process analysis at Group companies in Japan using Material Flow Cost Accounting (MFCA).
3R Initiatives
Initiatives by Kaneka
We are working on several initiatives to curb plastic waste emissions: (1) stabilizing manufacturing processes to improve yield; (2) process recycling of waste generated in manufacturing processes; (3) examining measures to prevent scale generation during plastic manufacturing; and (4) thorough sorting to recycle plastic waste. We are also working to reduce waste by converting plastic waste into valuable materials and to recycling plastic waste that would otherwise be outsourced for incineration.
Initiatives by Group Companies in Japan
Tobu Chemical Co., Ltd. is working to recycle vinyl chloride resin paste sol waste generated in the wallpaper manufacturing process. The initiative has receive a grant from the Ministry of the Environment after being chosen as a fiscal 2022 demonstration project for establishing a recycling system for plastics and other resources to support a decarbonized society. Previously, paste sol waste (around 200 tons/year) generated in the wallpaper manufacturing process has been incinerated. However, if paste sol waste, which is a mixture of vinyl chloride resin and diluent, is separated by distillation, the recovered diluent can be recycled as a raw material for wallpaper, while the vinyl chloride resin that is left over from distillation can be recycled as a raw material for PVC flooring. We are proceeding with the introduction of a recycling process for operation in fiscal 2023.
CHECK & ACT
For industrial waste, we will control waste generation to increase the recycling rate of waste from our operations at home and abroad.
Recycling Resources