北海道の地に、完全自動化の
医療機器プラントを新設する!
MEMBERS

- M.S.
- 1992年入社
苫東工場 Medical製造チーム
製造スタッフ
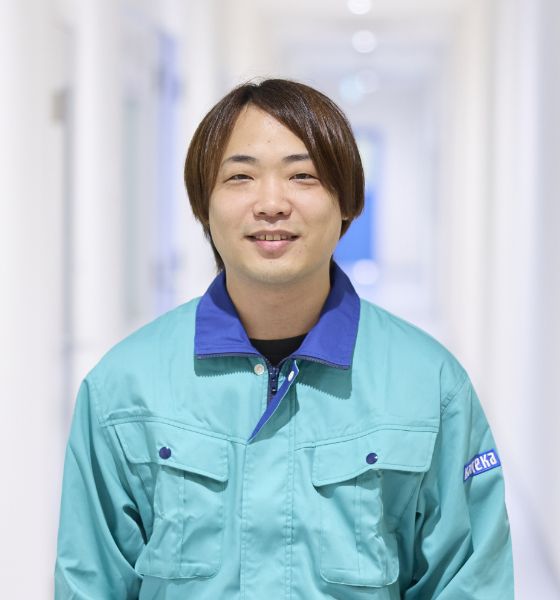
- M.W.
- 2009年入社
苫東工場 Medical製造チーム
製造オペレーター
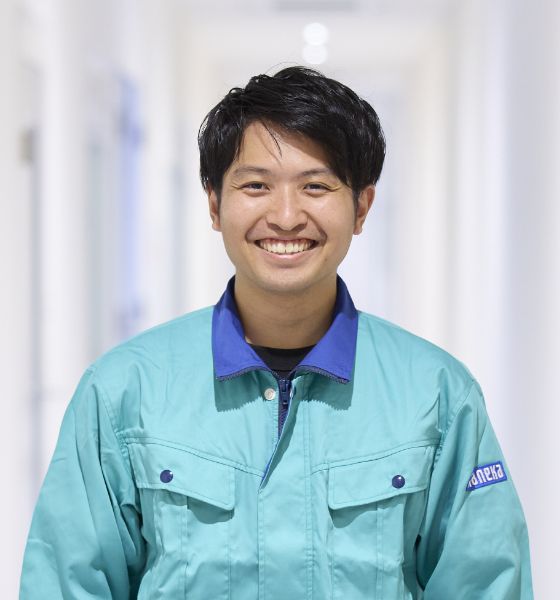
- T.N.
- 2013年入社
苫東工場 生産技術チーム
生産技術研究
- 所属部署および掲載内容は取材当時のものです
OUTLINE
ASO(閉塞性動脈硬化症)向け医療機器の需要が世界的に増加傾向にあるなか、カネカではそれらの製品を製造する既存工場の生産設備が、老朽化により更新時期を迎えていました。そこで持ち上がったのが、北海道における新たな医療機器プラントの開設計画。カネカにとって7カ所目、54年ぶりとなる国内事業場の新設プロジェクトに、「完全自動化」というテーマを掲げて挑んだ3人の現場担当者が、数年間にわたるチャレンジを振り返ります。
Phase_
まっさらの敷地の上に描く、自動化の夢。
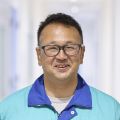
まずは本プロジェクトのチーム編成からですが、チームリーダーを務める私のもと、製造プロセス全般の技術開発を担う生産技術担当のT.N.くん、そして現場の職長として製造部署の立ち上げを担当してくれたM.W.くんという布陣。私としては、理想のメンバーをチームに招いたかたちだったので、実に心強かったです。
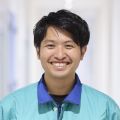
ポジションは違えど、3人とも大阪工場ではお互い業務連携していたので、気心が知れていました。
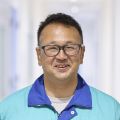
カネカはASO(閉塞性動脈硬化症)向けの医療機器として、吸着型血液浄化器「レオカーナ®」や吸着型血漿浄化器「リポソーバー®」といった製品を持っていますが、それらを作っているのが大阪工場。ただ、大阪工場は生産設備が老朽化しているという問題を抱えていた。一方で、今後はこれらの製品需要がアメリカや中国を中心に急拡大すると見込まれている。それなら、いっそのこと新工場を設立して、需要の増加に見合った供給基盤を確保しようということで、今回のプロジェクトが立ち上がりました。
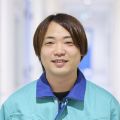
国内事業場の新設は54年ぶりと聞いて、これはやりがいがあるなと思いました。
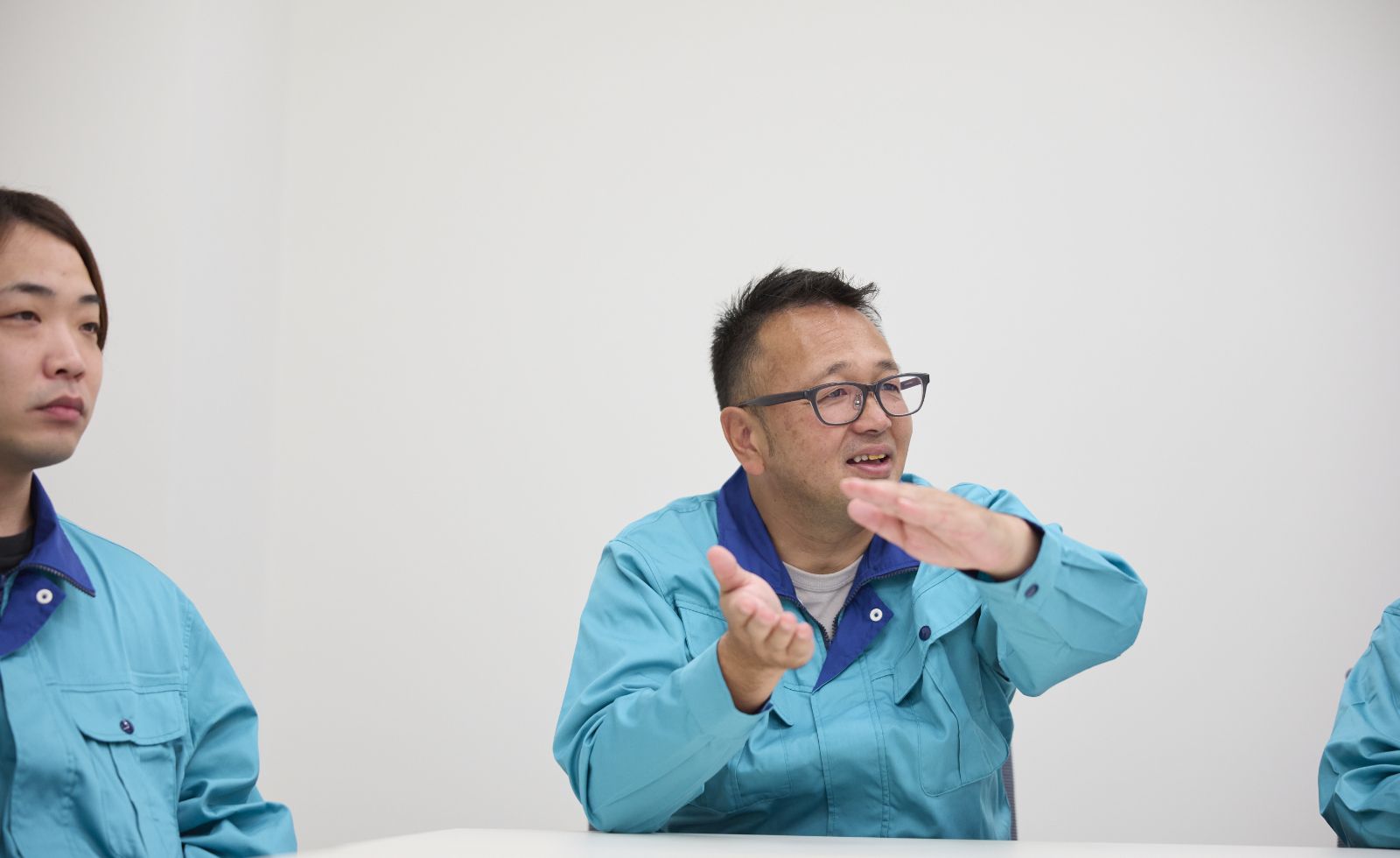
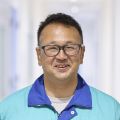
おそらくカネカ人生で一回きりのチャンス。なかなか経験できることではないと思う。
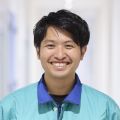
最初にプロジェクト参画の打診を受けたときは、正直言って、「自分しかいない」という気持ちでした。大阪工場でASO向け医療機器の生産技術をずっと担当してきて、自分が工程を一番よくわかっているという自負がありました。
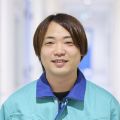
私はM.S.さんから「一緒にやろう」と直接オファーを受けて、うれしくて二つ返事でOKしました。
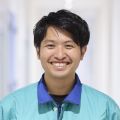
当時、職長は誰が来るかわからないという話だったので、私は「M.W.さんじゃないとだめだ!」と強く主張したんです。(笑)

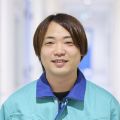
それ、素直に喜んでいいのかな?(笑) もう一つ大きなモチベーションにつながったのが、自動化の実現です。今回、この苫東工場では完全自動化を実現しましたが、これについては非常に思い入れが強かったです。カネカに入社して以来ずっと大阪工場で医療機器の製造に携わってきて、自分の中で「ここが自動化できたらいいのにな」「ここはもっと作業を簡略化できるのに」といったような「変えたい願望」が大きくふくらんでいたので、それをついに現実のものにできると思うと、ワクワクしました。
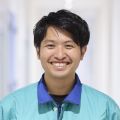
それは私も同感ですね。同じ自動化でも、現行の生産ラインありきの自動化ではなく、文字通りまっさらの敷地に自分たちが思い描いた自動化工程を一から組み上げることができるなんて、想像しただけでテンションが上がりました。
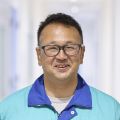
もちろんそのワクワク感の大きさに比例して、超えるべきハードルも高かったわけだけれど、みんなの「絶対に実現する!」という強い思いに支えられたチームとしての一体感が、プロジェクトを前へと進める強力な推進力になったと思う。
Phase_
理想の設備に向けて、課題をつぶしていく。
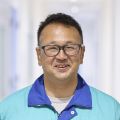
カネカ社内で本プロジェクトの実行が正式に決まったのが2021年の12月。翌2022年の1月には、プレス発表もしました。が実際には、その2年くらい前からT.N.くんたち生産技術メンバーを中心に、新工場設立に向けた構想の検討が始まっていました。
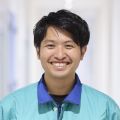
主には、原材料の形状の見直しでしたね。従来、口の部分がチューブになっている原材料を使っていましたが、チューブは柔らかいので個体によって形状がまちまちで、ロボットハンドにはつかみづらい。つかんだ後もぐにゃぐにゃと動くので扱いにくい。このままの形状では絶対に自動化は不可能だとわかっていました。
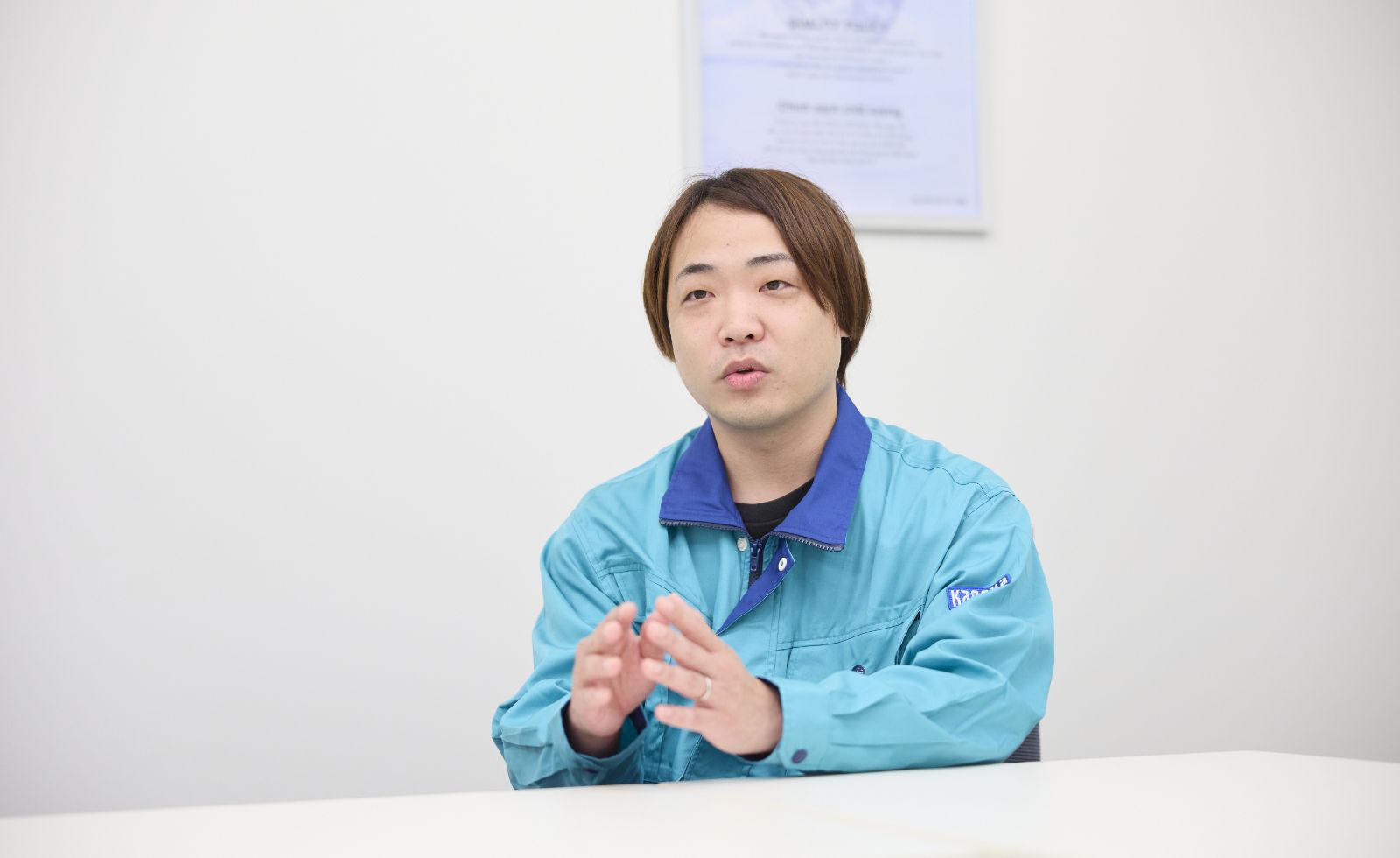
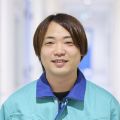
それを難なくできる人間とロボットの間には、今はまだ大きな差がある。
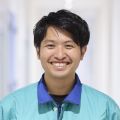
そう。その差を何とか埋めようとして、チューブから硬い樹脂素材を用いたものに変更できないかと考え、その方針で社内向けの提案資料を作成しました。
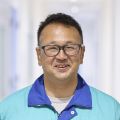
それ以外に、当初は手動で行う予定だった製品の梱包工程も自動化しようという話になり、最初から最後までフルに自動化した生産ラインを作るということで、社内決定した。そこで、さぁ、いよいよ本当にやるぞ、と気持ちが引き締まった。
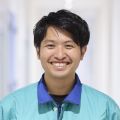
苦労したのはそこからですね。原材料の変更を提案したはいいけれど、今度はそれを実現しないといけない…。
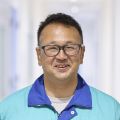
医療機器なので、重要なのは菌に対するシビアなリスク管理。万が一にも「菌が混入していました」は許されない。
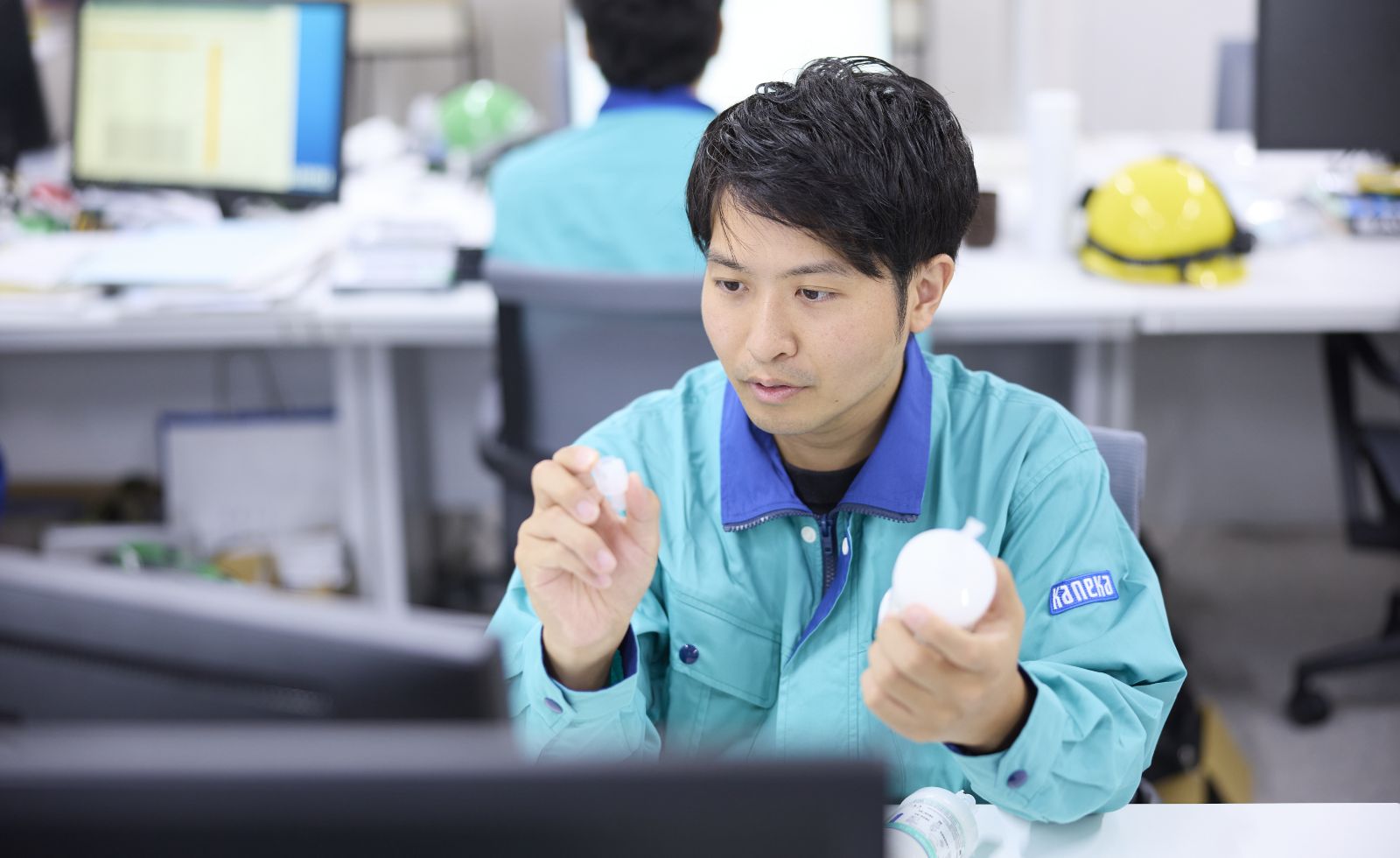
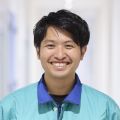
はい。原材料は滅菌した後、無菌状態になるのですが、問題はチューブから硬質素材に変える口の部分の加工。超音波を用いて振動させながら融着して密閉しようとしましたが、その生産設備の開発や条件出しには本当に苦労しました。それまでに培った基礎的なデータを分析する一方で、他部署の人にいろいろ聞いて知見を求めたり、設備メーカーの力をお借りして試行錯誤を繰り返したりしながら、何とか課題を解決することができました。
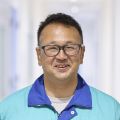
そうした肝となる要素技術開発に取り組みつつ、工程全体における現場作業の自動化についても整理していく必要があり、M.W.くんに検討を進めてもらいました。
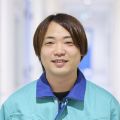
その頃、私はまだ大阪工場の製造現場で職長として普通に勤務していたので、通常業務をメインとし、サブ的にプロジェクト関連の業務に取り組んでいました。まず手がけたのは、自動運転フローの作成でした。個々の工程で具体的にどのような作業を行えばいいのか、一連の流れを細かく検討していきました。特にポイントになったのは、大阪工場でまだ自動化されていなかった工程。たとえば、人が目視で確認していた合否を、どのように自動化して機械に判定させるのか…。そうした課題を、T.N.くんたち生産技術メンバーと一緒に考えて解決していきました。
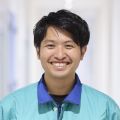
M.W.さんには、製造現場を預かる職長の立場から、ずいぶんいろいろとアイデアや要望を出してもらいました。
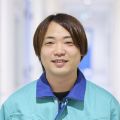
せっかく自動化するのだから、製造担当の自分たちが本当に使いやすい理想の設備にしたいという思いがあって…。T.N.くんも私たちの意見にちゃんと耳を傾けてプランに反映してくれるので、ありがたかった。
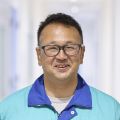
そうやってお互いにうまく連携することで、自動運転の全体フローや、それを可能にするための自動化装置のありようが、固まっていった。
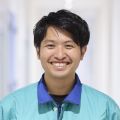
装置のレイアウトや機能については、仕様書の文面では表現しきれないことも多いので、設備メーカーのところに何度も足を運び、詳細にわたって議論を重ねました。実際に装置ができあがってから「こんなはずじゃなかった」という事態は絶対に避けたかったので、議論は決して怠らないように心がけました。
Phase_
二手に分かれての奮闘、そして現地で集結。
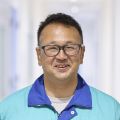
2023年の4月から、プロジェクトは次のフェーズに移りました。私は正式に北海道に異動となり、工場を建設する北海道苫小牧市の東部地域に赴任。カネカの建築班と合流して、工事内容の確認や現地受け入れ体制の整備などを進めました。
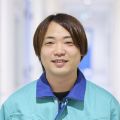
その頃は、まだ更地でした?
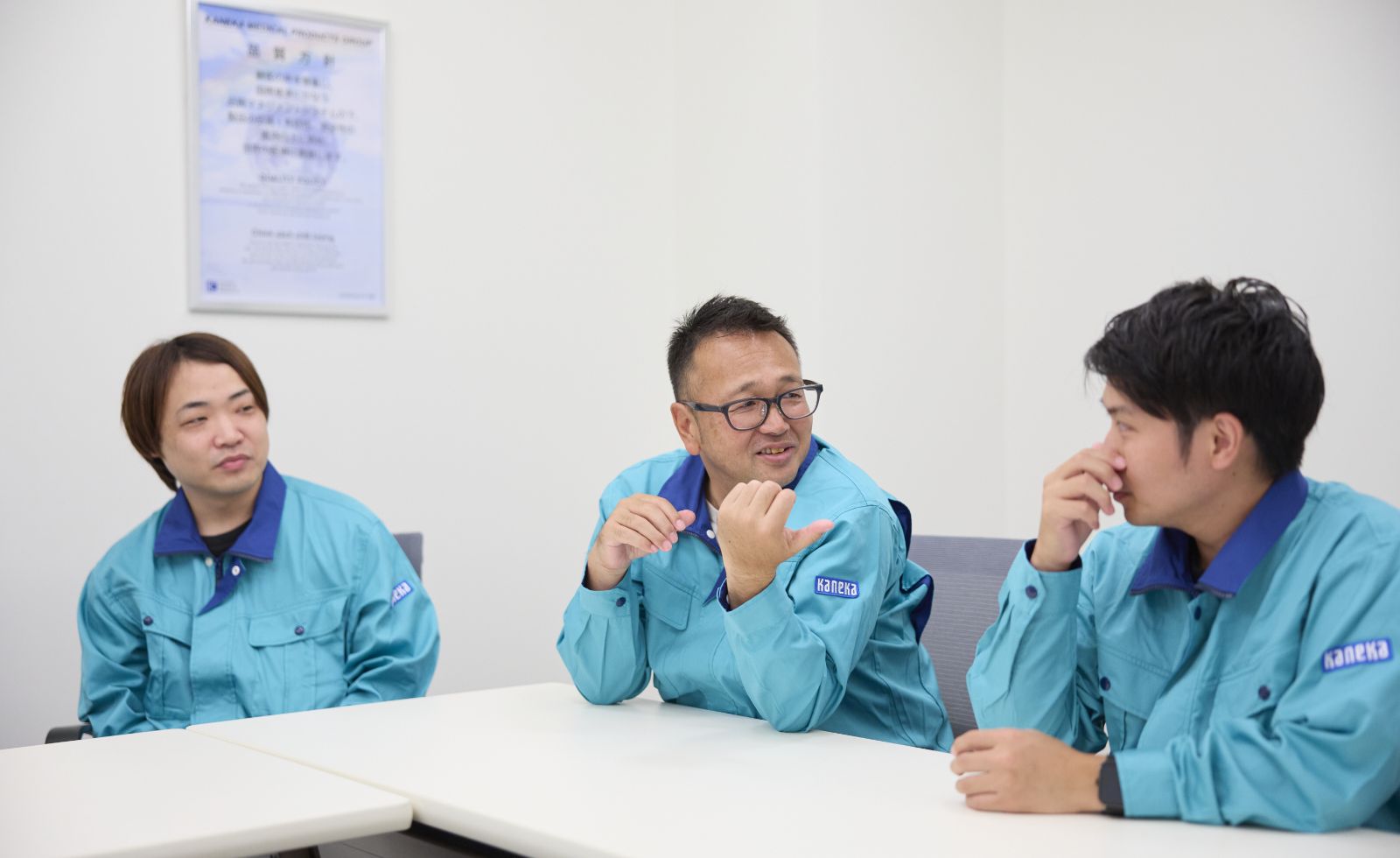
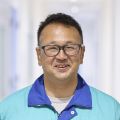
基礎ができあがったくらいかな。それを見て、感動した。もちろん更地のときにも出張で訪れてはいたけれど、そこに手が入って工事が進んでいるのを目にして、「本当にここに工場が建つんだ」と初めてちゃんと実感できた。もう何度そう思ったかわからないけれど(笑)、「もうやるしかない!」とあらためて気を引き締めなおした。
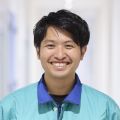
一方でM.W.さんと私は装置の仕上がり確認のため、彦根にある設備メーカーの工場に赴き、そこにプラン通りのレイアウトで実際に自動機を並べて試運転を実施しました。
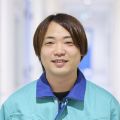
初回の試運転では、まったく思った通りに流れなかった。
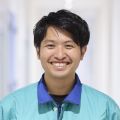
悲しいくらいに…。机上でとことん検討したつもりでも、やはり実機検証すると、想定外の課題がいくつも出てきました。たとえば、ある部材は成型時点でどうしてもコンマ数ミリ程度のばらつきが発生しますが、そのばらつきにロボットが対応できず、うまくハンドでつかめない…。想像以上にセンシティブであることがわかって、そこの調整に時間を要しました。
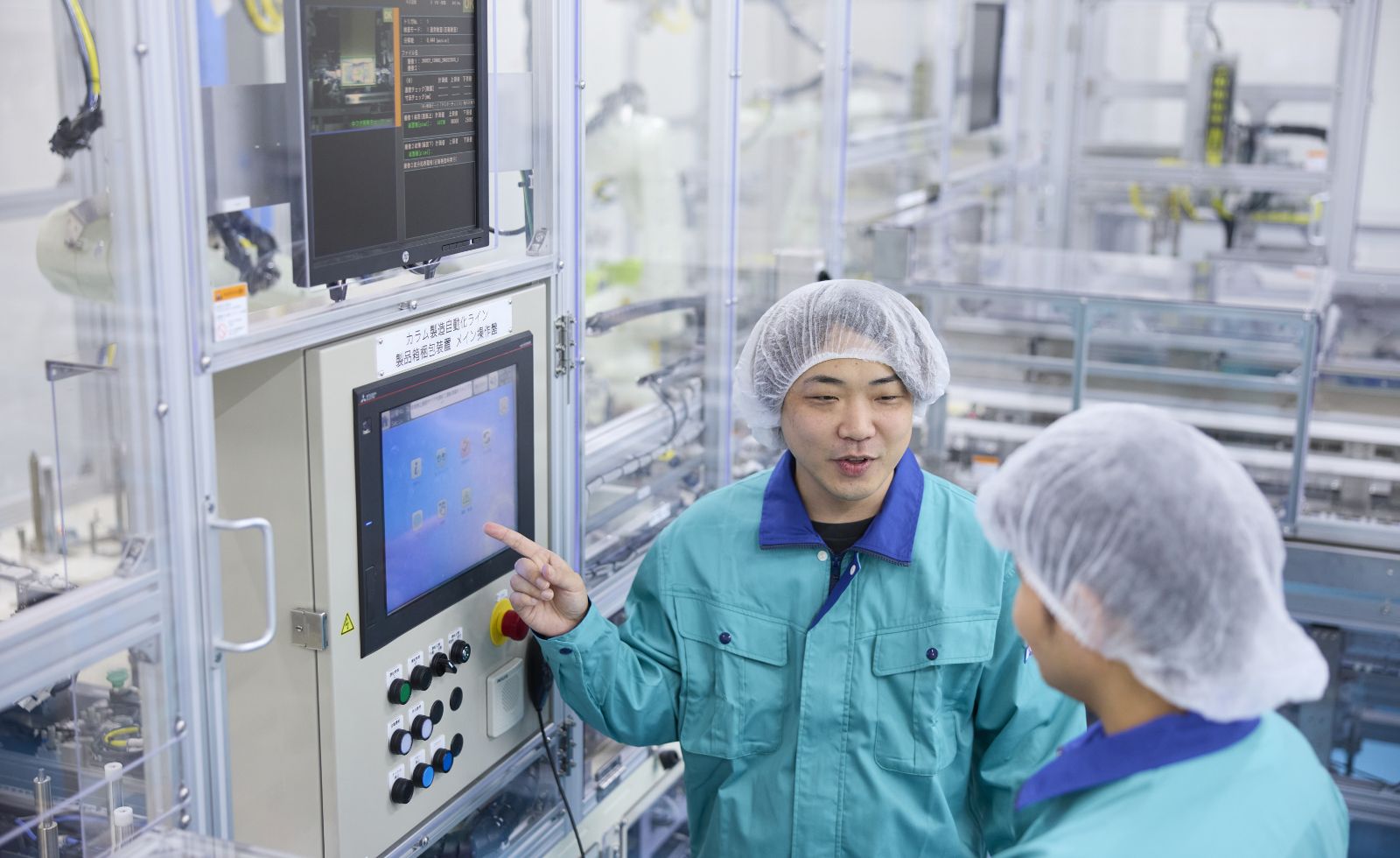
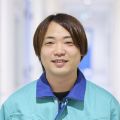
私は私で製造担当の視点から装置の動作を見て、「ここは、品質上こういうリスクがあるのではないか」といったように課題を洗い出し、設備やプログラムの作り込みに参加していました。ただメインは、どちらかといえば装置の操作習得と新人教育。この4月に、実際に新工場で製造を担当するメンバー5人が新たに入社してきたので、私と製造経験者3人が指導役となり、メーカーに操作方法を確認しつつ、新人メンバーに装置の扱い方や気をつけなければならないポイントなどを教えていきました。
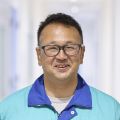
みんなには数カ月間、彦根にほぼ常駐するかたちで長期出張して奮闘してもらいました。その間に私は、工事の進捗確認のほか、原材料の調達に向けた凍結対策や危険物の取り扱い、輸送コストのアップなど、周辺課題の解決に取り組み、8月にはみんなを現地に迎え入れて最終フェーズへと突入していきました。
Phase_
現場を知り尽くしたメンバーの知識と技術の結晶。
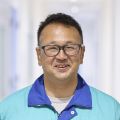
2023年8月、メンバーが北海道にそろい、事前の試運転を終えた装置も新工場に運び込まれ、据え付けられました。ここからは、実に密度の濃い半年間だった。予定されていたスケジュールで言えば、まずは年内の社内安全査察。これは、設備や製造手順などが安全性の観点から問題ないかどうかの社内チェックで、ここでGOサインをもらって、初めて設備メーカーから設備を引き渡してもらい、自分たちで機械を動かせる。続いて、翌年3月には外部認証機関の監査を受け国内販売承認を取得する必要がありました。プロジェクト開始時点ですでに2024年5月に稼働と発表しているので、それは死守しなければというプレッシャーのなかですべてを同時進行で動かしていった感じでした。
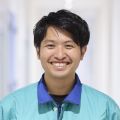
当初予定では、8月~10月がメーカーによる装置の試運転調整期間でしたが、もともと課題を積み残した状態で現地へ持ってきていたこともあり、2カ月で終わらず結局12月くらいまで調整が続きました。翌年3月の監査に向けて、10月にはバリデーション(製造方法などが適切かどうかの検証)を始める予定だったのが2カ月もずれこんでしまい、「この短期間で製造の条件出しができるか…?」と焦る気持ちでいっぱいでした。
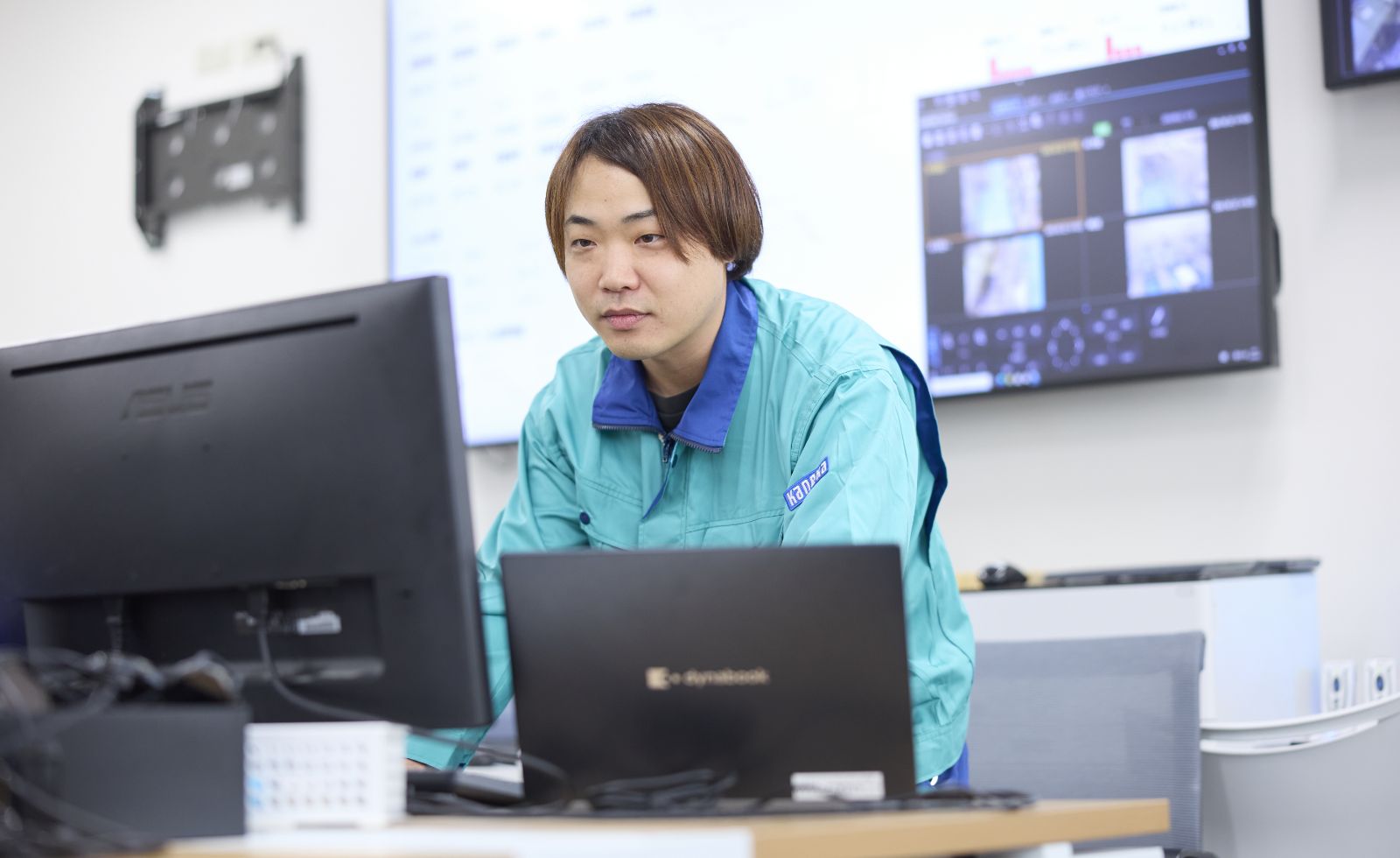
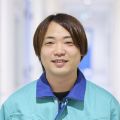
私たち製造メンバーは、設備の引き渡しが終わると、以降はすべて自分たちで操作しないといけないので、操作方法を覚え、作業標準書を作り、といった業務に忙殺されていました。あとはもちろん、引き続き新人教育もありました。
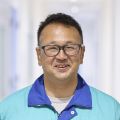
それで何とか社内安全査察は乗り切って、翌年の年明け早々から監査に向けたバリデーションをスタートさせた。ここから監査までの2カ月半は、まさに怒涛のスケジュールでしたね。
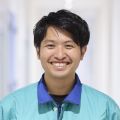
M.W.さんが作ってくれた作業標準書に則って、販売はしないものの実際に製品を製造して、求められる性能をクリアしているかどうかをチェック。もちろんすぐにうまくいくわけがないので、課題が出てきたらすぐにチーム内に共有し、メンバー全員で解決方法を検討してすぐ動き出す、ということを繰り返して製造条件を絞り込んでいきました。
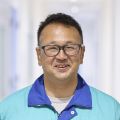
このときのチームワークは本当にすごかった。「必ず監査に間に合わせる」という思いを全員が共有して、一丸となって前に進んでいた。だからこそ、やり切れたんだと思います。
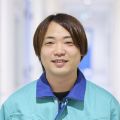
監査を受けて「指摘なし」という結果が出たときは、心からほっとしましたね。
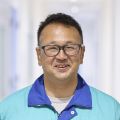
本当にそう。まだプロジェクトが終わったわけではないけれど、工場として一歩を踏み出せる資格をもらったことで安心できた。それからは、細かい不具合の対応や、作業手順の調整、人材教育などを引き続き進めて、5月の稼働、8月の開所式を迎えました。
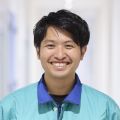
開所式は、会長をはじめ全役員のみなさんが顔をそろえたなかで執り行われたので、「やっとこの日が迎えられた」と胸にこみ上げてくるものがありました。
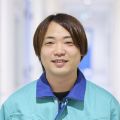
まだ海外での承認に向けた活動も続いていたので、バタバタしながらの当日でしたが、一つの区切りとスタート感は感じられましたね。
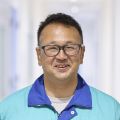
新工場立ち上げプロジェクトとしてはこれで一段落で、今は工場運営のフェーズに入っています。走り始めたばかりの工場なので、まだまだ解決しなければならない課題はありますが、今日に至るこの数年間を振り返ってみてどうですか?
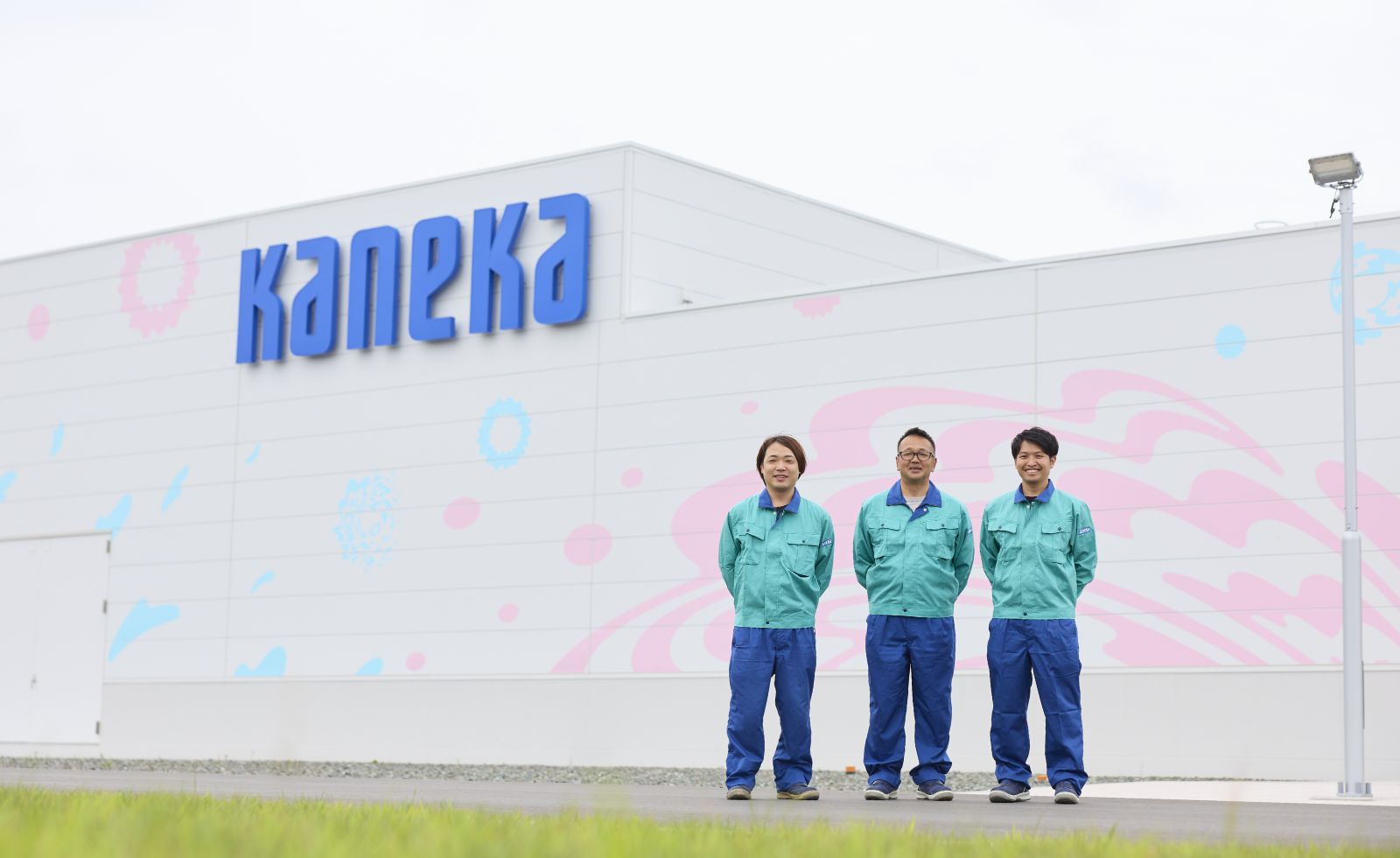
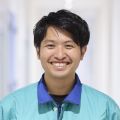
カネカの全工場を見渡してみても、全工程にわたって完全自動化を実現している例はまだ他になく、社内でも注目度が非常に高いように感じています。その完全自動化工程に、自分が考案した部材の形状や工程が反映され、その通りに製品が製造されている様子や、設計段階から検討を重ねてきた設備が正しく動作している姿を見ると、すべての苦労が報われたような気持ちでいっぱいになります。もうほとんど、わが子を見るような思いで眺めています。(笑)
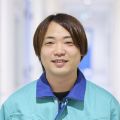
正直に言うと私は最初、「本当に完全自動化なんてできるのかな?」と心のどこかで疑う気持ちがありました。というのも、ずっと大阪工場で製造に携わるなかで、「医療機器の製品品質は、人が担保している」と思っていたからです。ところが、T.N.くんが情熱を注いで設備を作り上げていって、彦根で仮組みした装置群を見たときに「これなら本当に自動化ができるかもしれない」と、気持ちが切り替わりました。そこからは私も本気になって、それまで培ってきた知識と経験をフルに生かして取り組み、こうして無事に立ち上げることができたので、うれしい限りです。
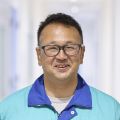
この新工場には、関係者それぞれの思いが詰まっていますね。私はと言えば、ずっと製造現場でキャリアを積んできたなかで、生産ラインに張りつくようにして神経を使う作業を行う、この医療機器の製造現場をどうにかしなければと思ってきた。それが実現して、一番最初の製品がパレットに乗って出荷口まで出てきたときは、本当に感無量でした。ここまでたどり着けたのは、もちろんここにいる3人だけではなく、建築班やエンジニアリング部門も含め、このプロジェクトに関わったメンバー全員が、それぞれの現場を知り尽くしていて、その知識・技術を最高のかたちで融合できたからだと思っています。まさに、これ以上ないチーム。みんなに感謝です。
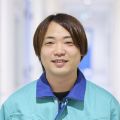
そのチームワークこそがカネカ、ですかね。
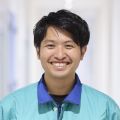
ですね!